3D printing is a modern technology that produces physical models layer by layer. It relies on CAD (computer-aided design) files to create complex shapes in a variety of materials.
Engineers can build prototypes and manufacturing parts with ease, eliminating the need for multiple set-ups and cutting production time. 3D printing also allows production to be done closer to the point of demand, reducing shipping costs and environmental impact. Contact By3Design now!
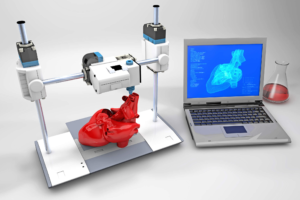
The rapid prototyping process allows engineers to build and test many iterations of the product, reducing the time needed for design development. Engineers can work on the 3D CAD model during the day, print and test a prototype parts or product overnight, then refine and adjust the design for another round of printing and testing. This cadence allows the team to incorporate actionable feedback from the client and collaborators to create a more effective and high-quality product.
The process also allows the team to create a prototype that looks real enough to gather genuine reactions from users and allow them to answer critical questions about their experience with the product. This can help them identify trends and themes that will need to be addressed in the next iteration. The team can then repeat the process with new prototypes and iterations until they have reached a point where the final product meets the desired user goals.
With the speed and ease of prototyping, it is important for the team to set clear goals about what they are trying to achieve with their prototype. This can be as simple as validating a concept or obtaining user feedback on usability and functionality. Keeping the goal in mind can save the company weeks or even months of time building and testing a prototype that won’t be successful in the marketplace.
There are several different types of prototyping processes available, each with its own advantages and disadvantages. In general, the quality of the finished product depends on the material used, the size of the part or object, and the complexity of the design. The range of materials available for rapid prototyping can vary from inexpensive plastics to more expensive metals, and the accuracy and tolerances achieved are dependent on the technology used.
Whether it’s creating scale models for the automotive industry or working with complex geometries and materials for the aerospace industry, rapid prototyping is an invaluable tool in the product-development process. It can greatly reduce the manufacturing time for a project, allowing teams to iterate on a design and produce high-quality prototypes to test and improve a product’s performance and usability.
Additive Manufacturing
Additive manufacturing is a technique that uses an additive process to create three-dimensional physical objects from a digital model. Its earliest applications were in prototyping, where CAD models were used to build physical models for testing and evaluating designs before going into production. However, it has since become an important technology for the manufacture of complex and lightweight parts in a variety of industries.
Using this technology, the engineer can produce a single component without the need for assembly, which is an important cost and time saver. Additionally, the engineer can design the part with geometric freedom, and not be limited by traditional manufacturing constraints. In some cases, the printer itself will generate the required geometry from a computer file, removing the need for labor and machine hours that would otherwise be spent on machining, drilling, and sanding.
The process begins with a digital model, which is then ‘sliced’ by the manufacturer’s software into layers that will be printed onto the printing material. The sliced model is then sent to the 3D printer, which will use its own proprietary software to lay each layer of the part on top of the other, creating the finished product. The layer-by-layer construction allows for the creation of a variety of shapes, including complex anatomical geometries.
This technique also enables the production of functionally-graded materials, where the internal architecture of a part can be designed to have different properties from its external appearance. This can be beneficial for medical applications, where a part’s inner structure can be made from a softer, more biocompatible material, while the outside is made from harder and stronger materials for mechanical performance.
Despite its numerous benefits, there are some challenges with this technology. While it has been used for decades in specific manufacturing industries, where the legal regimes of patents, industrial designs, copyrights, and trademarks apply, it is unclear how these laws will apply if 3D printing becomes more widely adopted by individuals or hobbyist communities. There are also concerns that it could lead to a proliferation of pirated goods, as the ability to quickly and easily print a copy is much easier than buying or leasing the original.
Additive Design
While traditional manufacturing relies on the reduction or subtraction of material — think cutting away sections of an alloy to make a bolt or hinge — additive printing is all about building up parts, layer by layer. It is a completely different way of making things and fundamentally changes the design process.
The etymology of the word “printing” comes from this approach: instead of cutting away bits of metal to create the desired shape, 3D printers add material on top of each other in layers to create the part. This is why it is considered additive, as opposed to subtractive machining or casting.
3D printers build objects layer by layer using a variety of materials, from polymers to ceramics to metals. Depending on the type of printer used and the material being printed, construction of the model can take hours or days. The time required to build a particular model also depends on the size and complexity of the design.
Once a model is constructed, it is often subjected to post processing and finishing to achieve final product properties. Post-processing and finishing can be as simple as a sanding or painting to improve surface texture or as elaborate as chemical vapor deposition of polymer, such as acrylonitrile butadiene styrene (ABS), to give the surface a hard, tenacious finish that resists wear and tear.
Compared to traditional fabrication methods, 3D printing provides greater freedom for designers and engineers in terms of geometry and performance. However, that is not a free-for-all: just like molding, casting, and machining, there are certain designs that are not suitable for 3DP. To ensure a successful design, it is critical to plan for printability.
For example, the geometrically complex features of a design may not be suitable for 3DP because they are too intricate and require a high degree of precision to be successfully printed. On the other hand, simple, repetitive features that are easy to fabricate, such as a pattern or grid, can be easily and quickly made with 3DP.
In order to maximize the benefits of 3D printing, it is important for manufacturers to train their employees on this emerging technology. This will enable them to use the technology efficiently, as well as to understand how to make improvements and adapt to the new process.
Material Jetting
Material jetting is a relatively new additive manufacturing process, and it is considered to be one of the most futuristic 3D printing technologies available today. This process uses a special UV-light to cure liquid photopolymer layers to build functional parts in a layer by layer fashion. The technology is currently being used in a variety of industries, including biomedicine and dentistry, as well as aerospace and manufacturing.
The main advantage of the material jetting process over other 3D printing techniques is its ability to print with multiple materials, and to combine both hard and soft (or opaque and transparent) materials in a single print job. This makes it easier to create complex shapes with internal structural elements that would be impractical or impossible to produce using other methods.
Unlike other additive manufacturing methods, such as SLA and SLS, which heat the raw material (which is in a liquefied form) with a laser, material jetting uses a UV-light to solidify droplets of printed material. The print head of the machine deposits these droplets on a platform that raises or lowers according to the height of each layer of the final product. Once the layer is complete, the UV-light is cured, and the platform drops again to expose a fresh drop of material. This process is repeated until the model is complete.
Like other additive manufacturing processes, material jetting can be slow, and the quality of the printed part may degrade over time if it is exposed to excessive UV light. However, this can be minimized by coating the prints with a protective UV-resistant material.
One of the most interesting applications for this technology is in medicine, where physicians and other medical professionals can use it to quickly fabricate prosthetics, hearing aids, artificial teeth, and bone grafts. There are even printers that can replicate models of tumors and other internal bodily structures from CT scans, allowing surgeons to better prepare for surgery. The ability to make these objects on demand means that patients no longer have to wait for months to receive the necessary equipment, and this can also help reduce inventory management costs and free up warehouse space.