Modern households and businesses rely heavily on appliances to keep daily routines running smoothly. From refrigerators and ovens to washing machines and air conditioners, these essential devices provide comfort, convenience, and efficiency. However, like all machines, appliances can experience wear and tear over time. When this happens, reliable appliance services for repair, maintenance, and installation become essential. These services not only restore functionality but also help extend the lifespan of appliances, ensuring they continue to operate at peak performance.
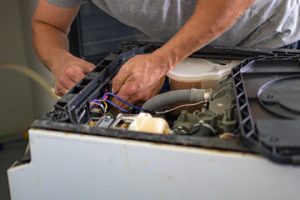
The Importance of Professional Appliance Services
Appliances play a crucial role in maintaining efficiency in homes and workplaces. When a major appliance breaks down, it can cause inconvenience, disrupt schedules, and sometimes even lead to costly damage. Professional appliance services ensure that these essential machines are repaired, maintained, and installed correctly to prevent further issues.
Some key reasons why appliance services are so important include:
- Restoring Convenience: A malfunctioning appliance can disrupt everyday routines. Prompt repairs bring life back to normal quickly.
- Ensuring Safety: Faulty appliances can pose safety hazards such as electrical issues, leaks, or overheating. Professional repairs reduce these risks.
- Saving Money: Regular maintenance and timely repairs prevent small issues from becoming expensive replacements.
- Improving Efficiency: Well-maintained appliances operate more efficiently, using less energy and lowering utility costs.
- Prolonging Lifespan: Professional care helps extend the durability of appliances, ensuring long-term performance.
Comprehensive Appliance Services
Professional appliance service providers typically offer a wide range of solutions designed to cover every stage of an appliance’s life cycle—installation, maintenance, and repair.
*Appliance Installation
Proper installation is the foundation for long-term performance. Even high-quality appliances may underperform if not installed correctly. Experts ensure that appliances are connected safely, leveled properly, and set up according to manufacturer specifications. This reduces the risk of future issues and guarantees optimal functionality from day one.
*Appliance Repair
When an appliance breaks down, repair services address the problem promptly and effectively. Skilled technicians diagnose issues accurately and provide solutions that restore the appliance to working condition. Common repairs include fixing leaks in dishwashers, addressing cooling problems in refrigerators, or resolving electrical issues in ovens and dryers.
*Appliance Maintenance
Routine maintenance is often overlooked, yet it plays a vital role in preventing unexpected breakdowns. Maintenance services include cleaning internal parts, checking electrical connections, replacing worn components, and ensuring appliances meet performance standards. Regular servicing helps avoid costly emergency repairs and improves energy efficiency.
Common Appliances Serviced
Appliance service providers handle a wide range of household and commercial equipment, including:
- Refrigerators and Freezers: Ensuring proper cooling and energy efficiency.
- Ovens, Stoves, and Ranges: Repairing heating elements, igniters, and control systems.
- Dishwashers: Addressing leaks, clogs, and poor cleaning performance.
- Washing Machines and Dryers: Fixing drainage issues, drum malfunctions, or heating problems.
- Microwaves: Handling electrical or mechanical faults.
- Air Conditioners and Heaters: Maintaining proper climate control and energy efficiency.
Benefits of Hiring Reliable Appliance Services
While some people may attempt do-it-yourself fixes, professional appliance services provide significant advantages:
- Expert Knowledge: Trained technicians have the skills and experience to handle complex issues across different types of appliances.
- Safety Assurance: Professionals follow safety protocols to prevent hazards such as electrical shocks, gas leaks, or water damage.
- Time Efficiency: Appliance experts complete repairs quickly, minimizing disruptions to daily life.
- Access to Tools and Parts: Service providers often have specialized tools and genuine replacement parts that may not be easily available to the average consumer.
- Guaranteed Results: Professional services often come with warranties or service guarantees, offering peace of mind.
Signs You Need Appliance Services
Recognizing the signs of appliance issues early can help prevent major breakdowns. Common indicators include:
- Unusual noises or vibrations.
- Increased energy bills without changes in usage.
- Leaks, sparks, or smoke.
- Inconsistent or insufficient performance.
- Frequent cycling on and off.
- Difficulty starting or shutting down appliances.
When these symptoms occur, it is best to call a professional rather than risk worsening the problem through temporary fixes.
Preventive Care and Long-Term Savings
Preventive maintenance is one of the most cost-effective strategies for managing appliances. Regular check-ups ensure that appliances are running efficiently and reduce the likelihood of emergency repairs. For example, cleaning refrigerator coils improves cooling efficiency, while inspecting dryer vents reduces the risk of fire hazards.
By investing in maintenance, homeowners and businesses save money in the long run by avoiding costly replacements and reducing energy consumption.
Choosing Reliable Appliance Services
With many options available, selecting the right appliance service provider is essential. Here are some factors to consider:
- Experience and Training: Providers with years of expertise are more likely to deliver reliable results.
- Range of Services: A comprehensive provider can handle installation, maintenance, and repair for multiple appliance types.
- Transparency: Clear pricing and honest assessments build trust and prevent hidden costs.
- Customer Support: Reliable providers offer responsive communication and flexible scheduling.
- Reputation: Reviews and referrals provide valuable insight into the quality of service.
The Role of Professional Services in Sustainability
Reliable appliance services not only benefit property owners but also contribute to environmental sustainability. Well-maintained appliances consume less energy and water, reducing environmental impact. Repairing rather than replacing appliances also minimizes waste and the demand for new manufacturing.
Appliances are essential to modern living, and keeping them in top condition requires reliable services for repair, maintenance, and installation. Professional technicians provide the expertise, safety, and efficiency needed to ensure appliances continue operating at their best. By investing in professional care, property owners save money, extend the lifespan of their appliances, and enjoy greater peace of mind. Whether it’s setting up a new device, restoring a broken one, or performing routine maintenance, reliable appliance services are the key to keeping households and businesses running smoothly.